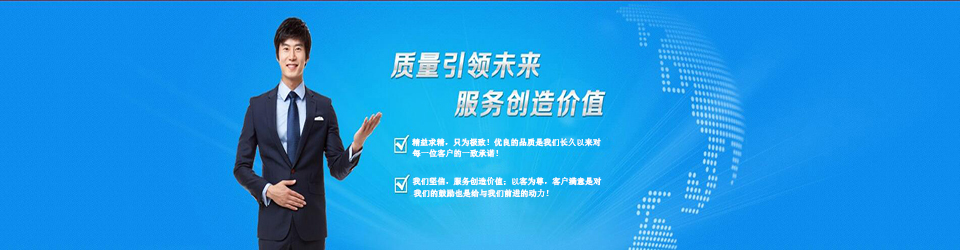
除尘器系统管网阻力平衡方法
除尘器系统管网阻力平衡方法
图9-彳0阻力系数与曲率 在设计的除尘系统中,当将若干个尘源点连接起
1' 2' 3, 4—来并组成一个餘尘系统时,必然有三通管,这时必现 考虑在三通管处两个支管的姐力平衡问题,两支管之 间阻力差不应大于如不平衡,对于阻力较大的支管,应通过加大管径来减小阻力. 使两支路阻力平衡。
1.管网平衡方法
除尘系统的管网设目前广泛采用的是静态阻力平衡法,即根据假定流速得到初歩的 管网结构,计算所有管段的阻力损失,再对每个并联节点进行阻力平衡计算,如果不平衡率
小于10%s则认为达到设计要求。用这种方法获得的管网系统,实际的不平衡率与理论计 算相差较大i部分抽风点不能达到除尘要求。采用动态平衡法对管网结构进行优化调整,系 统的阻力平衡计算又快又好,在保证除尘效果的同时,还能大大地提高工作效率。
开口比A 古—4 h/D<$ o c i i i i•~^ > c
!i vo t> oo o > d o* o c
1 1 1 .…1N O 1
面积比n »n :oo-….<2 Sh/S^. m u- n/ o o o c^ rr-* .‘cst 1-H o M
% '(jD 1^-00 1^ g 《: O 0*0 0 t3 O
o
®s-m插板阀的阻力系数与开度
已知各抽凤点设计风量的条件下,管网大致走向e经确定,要求设计管道直径并确定阀 nr开度。而校核计算是对现有除尘系统的运行状况进行分析。对一个运行工况不良的除生系 统,通过校核计算和分析,找出不利因素,提出改进或调整原系统结构的优化方案,使其达 到预期的运行效果。
對并联管路进行阻力平衡。一般的通风系统要求两支管的阻力差不超过15?1,除尘系 统要求两支管的阻力差不超过10%,以保证各支管的风量达到设计要求。
当并联支管的阻力差超过上述规定时,可用下述方法进行阻力平衡。
CD调整支管管径这种方法是通过改变管径,即改变支管的阻力#达到阻力平衡的。 调整后的管径按下式计算:
(m)
式中¥ 为调整后的管径,m; D为原设计的管径,m; Af为原设计的支管阻力. Pa,, 为为了阻力平衡,要求达到的支管阻力,Pa。
鹿当指出,采用本方法时不宜改变三通支管的管径,可在三通支管上增设一节渐扩 (缩)管,以免引起三通支管和直管局部阻力的变化。
CI)增大排风量当两支管的阻力相差不大时(例如在20%以内 >,可以不改变管径, 将阻力小的那段支管的流量适当增大,以达到阻力平衡。增大的排风量按下式计算:
Q,=Q(厶夕 7A/>3^S (m3/h)
式中,CT为调整后的排风量,m3/h; Q为原设计的排风量,m3/h; Ap为原设计的支 管阻力,Pa; A//为为了阻力平衡,要求达到的支管阻力,Pa。
(3)增加支管阻力阀门调节是最常用的一种增加局部阻力的方法,它是通过改变阀 门的开度,来调节管道阻力的。应当指出,这种方法虽然简单易行,不需严格计算,但 是改变某一支管上的阀门开度,会影响整个系统的压力分布。要经过反复调节,才能使 各支管的风量分配达到设计要求。对于除尘系统还要防止在阀门附近积尘,引起管道 堵塞。
管网平衡步骤如下:根据已知的设计参数获得初步的管网结构,在此基础上求解系统的 风量分配;然后,软件将对获得的风量分配进行分析比较(实际风量与设计风量的偏差是否 超过土拔%),判断系统是否平衡。如果系统不平衡,则通过调整管网结构重新计算风量分 配。如此反复,最后求得平衡的除尘管网。
1. 除尘管网平衡实例
(1)除尘系统概述该除尘系统共有20个除尘点,设计采用负压除尘设备系统。系统 的主要组成部分有:风机1台,布袋除尘器1台,消声器1台及除尘风管等,管网中共有 42根管段,拥个抽风点,餘尘系统流程为:尘源—抽风管网—除尘器—风机—消声器—排 放烟囱。
系统的主要设计参数为:系统总风量122400m3/h;设备阻力,袋式除尘器ISSOPa,消 声器lOOPa;系统漏风率,管网10輝,负压设备5%。
根据软件要求,需绘制该系统的水力计算草图,并进行管段编号,如图9-13所示。
(2)除尘系统能耗计算将整理好的管网参数输入到程序中,假定各管段初始流速,计 算后得到初步的管网结构参数;根据这个初步的管网结构,求解各管段的实际风量分配,结 果如表9-5所示。为便于观察比较,这里只将风量偏差4超过士 10%的管段数据列表。
管段
编号设计风量 /(m3/h)流速
/(m/s)阀门开度 /(。)管径 / mm实际风量 /(m3/h)风量偏差率 A/%
I1200014. 66050010354. 02— 13. 72
2480013. 4203203882. 65-19. 11
31680013. 99
60014236. 67-15. 26
52100014. 72—67018667. 85— 11. 11
6420018. 3503004667.9611. 14
19600022. 9503608403. 8740. 06
22540013. 5403404423.85-18.08
24900015.73-4207839. 25— 12. 90
25360020. 4902804539. 7326. 10
27840014. 7504207353. 72— 12.46
28420013, 1103003333. 47— 20. 63
M1260015. 13•—50010637, 19-15.18
36600021. 8403607998. 4133. 31
371440019. 38-56017179. 3619. 30
这个风量分配情况是根据假定流速法确定的,在没有采取改进措施前,管网阻力平衡性 较差,必然导致风量分配不合理。从表9-5可知,处于各子网末端的管段1~3、22、24. 27~29,其风量偏差率均普遍偏大(超过一 10%),这些点的除尘效果较差,且流速较低, 容易造成管道积灰。考虑系统管网和负压设备的漏风率,系统最初的总风量为141372m3/h, 系统压力损失为3380Pa。
根据风机电机功率计算方法求得改除尘风机功率约为194. 7kW»采用前述两种方法改 进系统后的风机电耗情况如下。
①增大系统总风量。根据表S-6中的数据,管段28的风量负偏差最大。为使管道28的 风量偏差率达到±10%内,经反复模拟,系统总风量需增大11. 3%左右,即增大后的总风 量为 160000 m3/h。
表9-6增大系统总风量的风量分配(部分管段)
管段
编号设计风量
/(m3/h)流速
/(m/s)阀门开度
1C)管径
/mm实际风量
/ (m3/h)风量偏差率
A/Y,
11200016. 59050011718.33—2. 35
2480015.1803204394. 25—8. 45
31680015.84-60016112.57-4.09
52100016. 65-67021127.630, 61
6420020.7703005283. 0425.79
19600025. 9703609511. 2158.52
22540015. 3303405006.76—7. 28
24900017. 80-4208872. 19-1.42
25360023.1902805137. 9142. 72
27840016. 7004208322. 69—0. 92
28420014. 8303003772. 71-10. 17
291260017. 12-50012095. 40—4. 0
36600020. 84036010390. 6850. 87
371440024. 72—5609052.3335.02
表M是增大系统总风量后得出的岚量分配情况。很明显,所有风量偏差为负的管段均 达到了既定的风量要求,除尘效果好;但是,风量偏大的管段不仅数量增多(4>105的 管段有23个,表9-6未全部列出),而且偏差率更大,最高的为管段If,达到58.52妬。正 如前所述,这部分管段可能抽走有用物料,流速变大而导致管道磨损加剧。风量加太岳系统 压力损失相应增大为445gPa,功率增大为2MkW,相比于原来的系统增大了近。
相关资讯
- 高温除尘布袋的使用性能及优点
- 除尘布袋市场未来发展空间大
- 褶皱滤袋清灰效果到底怎么样
- 如何防止脉冲布袋除尘器漏风
- 脉冲布袋除尘器的这些特点你了解多少
- 脉冲布袋除尘器清灰不彻应找这几方面
- 脉冲布袋除尘器袋笼安装方法及步骤
- 什么原因导致除尘布袋老化
最新产品
同类文章排行
- 如何防止脉冲布袋除尘器
- 脉冲布袋除尘器的这些特
- 脉冲布袋除尘器清灰不彻
- 脉冲布袋除尘器袋笼安装
- 脉冲布袋除尘器的操作管
- 布袋除尘器的简单介绍
- 带你了解脉冲除尘器除尘
- 降低布袋除尘器压力损失
- 带你了解脉冲除尘器除尘
- 袋式布袋除尘器对于环境